Cutting wait times at automotive plants for dry-van carriers
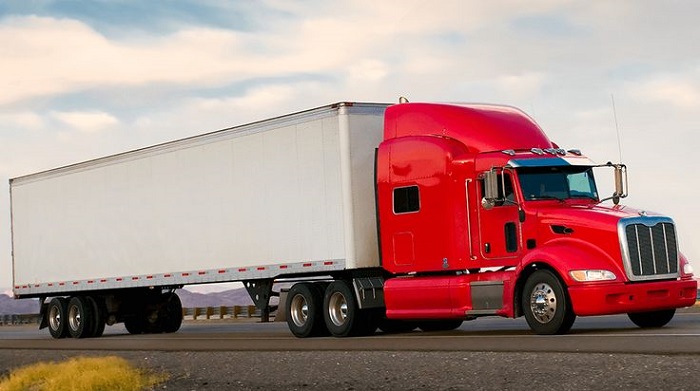
Automotive plant freight at Detroit OEM docks faces unique challenges that impact dock efficiency and overall supply-chain uptime. Dry-van carriers play a critical role in just-in-time (JIT) scheduling, yet long dwell times and congested trailer pools often create bottlenecks. Inefficient yard jockey movements and limited visibility without RFID tags further exacerbate delays. These issues not only increase carrier wait times but also disrupt production flow. Addressing these challenges is essential for optimizing dock operations, improving freight throughput, and maintaining the high standards required in automotive manufacturing environments. This article explores effective strategies to cut wait times and boost efficiency.
2. Leveraging Check-in Apps to Streamline Dry-Van Operations
Integrating check-in apps into automotive plant freight processes at Detroit OEM docks offers a transformative solution to reduce dry-van carrier wait times and enhance dock efficiency. These digital tools enable carriers to preregister their arrival, providing real-time updates that align with the plant’s JIT schedule. By automating check-ins, check-in apps minimize manual paperwork and eliminate unnecessary dwell time, allowing yard jockeys to manage trailer pools more effectively. Additionally, when paired with RFID tags, these apps improve visibility across the supply chain, enabling precise tracking of vehicles and cargo. This increased transparency helps docks anticipate congestion and optimize trailer staging, ensuring smooth, timely turnarounds. Ultimately, leveraging check-in apps supports a seamless flow of dry-van shipments, significantly boosting supply-chain uptime and reducing costly bottlenecks at Detroit OEM facilities. Embracing this technology is a critical step toward achieving operational excellence in automotive logistics.
3. Drop-and-Hook Strategies to Minimize Dwell Time and Boost Dock Efficiency
Implementing drop-and-hook strategies at Detroit OEM docks is a proven method to slash dwell time and elevate dock efficiency for automotive plant freight. Key elements include:
- Pre-Positioned Trailer Pools: Maintain ample trailer pools near the dock, allowing yard jockeys to swiftly swap loaded trailers with empty ones without waiting for unloading, aligning perfectly with the JIT schedule.
- Optimized Trailer Staging: Use RFID tags to track trailer locations in real time, enabling seamless coordination and quick trailer retrieval, which reduces idle time in the yard.
- Driver Flexibility and Training: Encourage dry-van carriers to adopt drop-and-hook protocols through clear communication and training, minimizing delays caused by unfamiliarity with procedures.
- Coordinated Scheduling: Synchronize carrier arrivals and trailer availability via digital platforms and check-in apps to prevent congestion and ensure a continuous flow of trailers.
- Yard Jockey Efficiency: Empower yard jockeys with real-time data to prioritize trailer swaps and move trailers promptly, cutting unnecessary movements and wait times.
By integrating these drop-and-hook tactics, automotive plants can significantly reduce carrier wait times, streamline dry-van operations, and maintain vital supply-chain uptime. This strategy is essential for Detroit OEMs striving for operational excellence and high dock throughput.
4. Appointment Scheduling Hacks for Just-In-Time (JIT) Supply-Chain Uptime
Optimizing appointment scheduling is pivotal for maximizing dock efficiency and reducing dwell time at Detroit OEM automotive plant freight operations. Using digital scheduling platforms integrated with RFID tags, plants can enforce strict JIT schedules that stagger dry-van carrier arrivals to avoid congestion and overloaded trailer pools. Automated reminders and real-time updates empower yard jockeys to anticipate incoming trailers, ensuring swift trailer swaps and minimizing idle time. Additionally, dynamic rescheduling capabilities accommodate unforeseen delays, maintaining steady supply-chain uptime. Collaborative communication between carriers and plant schedulers further refines appointment accuracy, preventing bottlenecks on the dock. By adopting these appointment scheduling hacks, automotive plants can synchronize dry-van movements seamlessly, cutting wait times and driving continuous throughput in demanding JIT environments.
5. Utilizing RFID Tags and Trailer Pools for Real-Time Yard Jockey Coordination
- Real-Time Tracking with RFID Tags: Equip trailers with RFID tags to instantly locate and monitor assets within trailer pools, enhancing visibility across the yard.
- Streamlined Yard Jockey Dispatch: Provide yard jockeys with live updates on trailer status and location, enabling faster, data-driven movements aligned with the JIT schedule.
- Efficient Trailer Pool Management: Use RFID data to optimize trailer staging and reduce dwell time by quickly identifying trailers ready for drop-and-hook.
- Improved Dock Efficiency: Minimize idle time by coordinating yard jockeys’ activities based on accurate, real-time information from RFID-enabled trailer pools.
- Enhanced Supply-Chain Uptime: Synchronizing RFID tracking with yard operations supports smoother dry-van carrier flows, critical for Detroit OEM automotive plant freight demands.
6. Case Studies: Success Stories from Detroit OEM Facilities
Several Detroit OEM automotive plants have successfully cut dry-van carrier wait times by embracing integrated strategies that enhance dock efficiency and supply-chain uptime. At one major facility, implementing check-in apps combined with RFID tags in trailer pools enabled real-time tracking of incoming shipments. This innovation reduced dwell time by 30%, allowing yard jockeys to coordinate trailer swaps precisely within the JIT schedule.
Another plant adopted a rigorous drop-and-hook system supported by dynamic appointment scheduling. By synchronizing carrier arrivals and trailer availability digitally, the plant minimized congestion on the docks and improved dry-van turnaround by 25%. Operators noted smoother yard jockey dispatch and faster trailer staging, directly boosting overall throughput.
A third facility focused on comprehensive training for drivers and yard staff alongside technology upgrades. Clear communication around drop-and-hook protocols, coupled with RFID-enabled trailer pools, cut manual check-in delays and informed yard jockey movements. The result was a 20% increase in dock efficiency and a more predictable supply chain.
These case studies demonstrate how Detroit OEM automotive plants can leverage technology and refined processes to dramatically reduce carrier wait times, optimize freight flow, and uphold stringent JIT schedules critical to automotive manufacturing success — creating real advantages for anydriver operating in the region.
7. Conclusion: Driving Continuous Improvement in Dock Efficiency for Dry-Van Carriers
Reducing wait times at automotive plants is crucial for maximizing dry-van carrier productivity and cost-efficiency. By analyzing root causes — such as scheduling bottlenecks, inefficient dock processes, and communication gaps — carriers and plants can implement targeted solutions. Leveraging technology like real-time tracking, automated check-ins, and data-driven scheduling optimizes dock workflows and enhances transparency. Collaborative partnerships foster proactive problem-solving and continuous feedback loops, ensuring improvements are sustainable. Ultimately, committing to ongoing process refinement not only slashes wait times but also boosts carrier reliability and plant throughput. Dry-van carriers who prioritize dock efficiency gain a competitive edge, delivering faster turnaround and exceptional service in the demanding automotive supply chain landscape.